Aker Arctic provides ice expertise for Canadian Polar Icebreaker
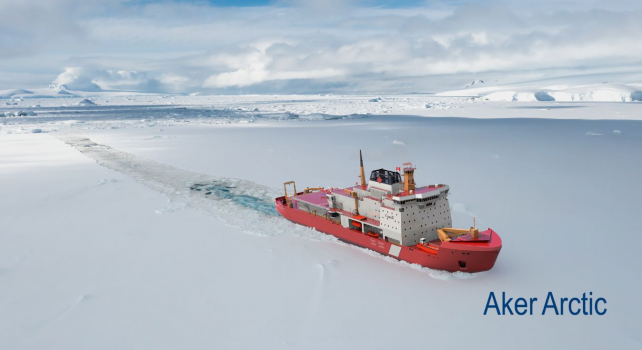
The Canadian Polar Icebreaker project, originally initiated in 2012, resumed two years ago. Aker Arctic has continued to provide its expertise in Arctic ship design to ensure the vessel meets the latest technical developments in icebreaking.
The Government of Canada is moving forward with the construction of two Polar Icebreakers that will replace Canada’s existing largest icebreaker, the CCGS Louis S. St-Laurent. The first Polar Icebreaker is due for delivery in 2030 and will be built by Seaspan Vancouver Shipyards.
Larger and more powerful than current Canadian icebreakers and, in fact, one of the most capable icebreakers in the world, the new vessels will enable the Canadian Coast Guard to conduct year-round operations in Canada’s Arctic. Their improved capabilities will ensure they can operate at higher latitudes for longer periods, allowing better support for northern Canada, while advancing high Arctic science and providing a faster response to maritime emergencies.
Part of the design team
When the Canadian government awarded the design contract to STX Canada Marine in 2012, Aker Arctic was part of the design team developing the Polar Icebreaker for the Canadian Coast Guard and providing support on icebreaking-related issues.
“As the original vessel design was developed nearly a decade ago, technology has since taken leaps forward, particularly in propulsion systems and hull construction,” says Mika Hovilainen, head of ship design at Aker Arctic Technology.
In 2021, Aker Arctic’s experts teamed up with Seaspan Vancouver Shipyards and another Finnish design company, Elomatic, for a thorough design check and update of the Polar Icebreaker design.
Design check of concept
The overall aim is to build a modern and effective icebreaker which responds to future requirements and fulfils its complex mission profile.
The project thus began with a review of the vessel concept, aiming to investigate possible improvements in the design and to ensure that the vessel incorporates the latest technology.
“Essential parts of this investigation were identifying possibilities to reduce technical risks and evaluating improvement opportunities,” Hovilainen explains.
An additional target was optimising the design for construction.
Efficient propulsion system
In the next phase, contract design options (CDO), three different propulsion options were evaluated.
“In a joint workshop with the Canadian Coast Guard, a hybrid propulsion configuration, incorporating two azimuthing propulsion units for optimal manoeuvrability and a centre shaft-line for efficiency during long transits in heavy ice, was proposed,” Hovilainen continues.
An extensive set of model tests in ice and open water were completed to verify seakeeping, manoeuvrability, and the enhanced performance, all with fulfilling results.
Steel hull improved with nonlinear analysis
Nonlinear analysis provides a more insightful method to calculate a vessel’s primary structures, including a better understanding of the safety margins present in the design. When the exact point of failure is known, contrary to traditional linear analysis, unnecessary steel structures can be reduced and other vulnerable structures strengthened, to improve the overall structural design of the vessel.
The steel hull of the new Canadian polar icebreaker has been optimised with the help of Aker Arctic’s nonlinear analysis tools. The result is a lighter ship with many benefits; for instance, lower steel weight, reduced construction costs, and an efficient steel structure. (Read more in our article explaining nonlinear analysis.)
“Some special materials have also been substituted to streamline construction work, such as extra high tensile steel,” adds project manager Jukka-Pekka Sallinen at Aker Arctic.
Optimising the design
During the past year, the conceptual design material has been updated jointly with Vard Marine, Elomatic, Canal, Barrier Marine Services, Knud E. Hansen, and Seaspan Vancouver Shipyards.
“The final construction engineering design phase is now ongoing with functional design soon to be followed by production design,” Sallinen says.
In addition to providing continuing support to Seaspan’s design team, Aker Arctic’s experts are responsible for the Polar Icebreaker’s hull form, ice strengthening of the hull structures, performance, stability, and winterization.
Supervising role
Aker Arctic has also supported the shipyard’s Technical Authority team supervising the ship design to ensure that all fundamental aspects of the design, such as owner’s requirements, cross-discipline integration, and safety, are taken into account.
“The design documents are verified to ensure that aspects related to operation in low ambient temperatures and ice-covered waters are incorporated properly, as this is our core expertise,” underlines Jillian Adams, team leader for structural design at Aker Arctic.
Prototype block to test processes
Before full-rate construction on the Polar Icebreaker begins, Seaspan has been developing a prototype block to pilot the new systems, processes, people, and tools that are required to work with the heavy structures necessary to manufacture a Polar Icebreaker. Some of this steel will be up to 60 millimetres thick, to enable the ship to safely navigate through the multi-year ice it will encounter in the Arctic.
In May 2023, Seaspan reported that the prototype block construction had begun. The lessons learned from building the block will be used to help improve the quality and efficiency of the process for designing and manufacturing the vessel when full production begins in late 2024.
Photo: Aker Arctic