The green transition goes from global customers to Koja’s production: “We want to be the technology and environmental leader in our industries”
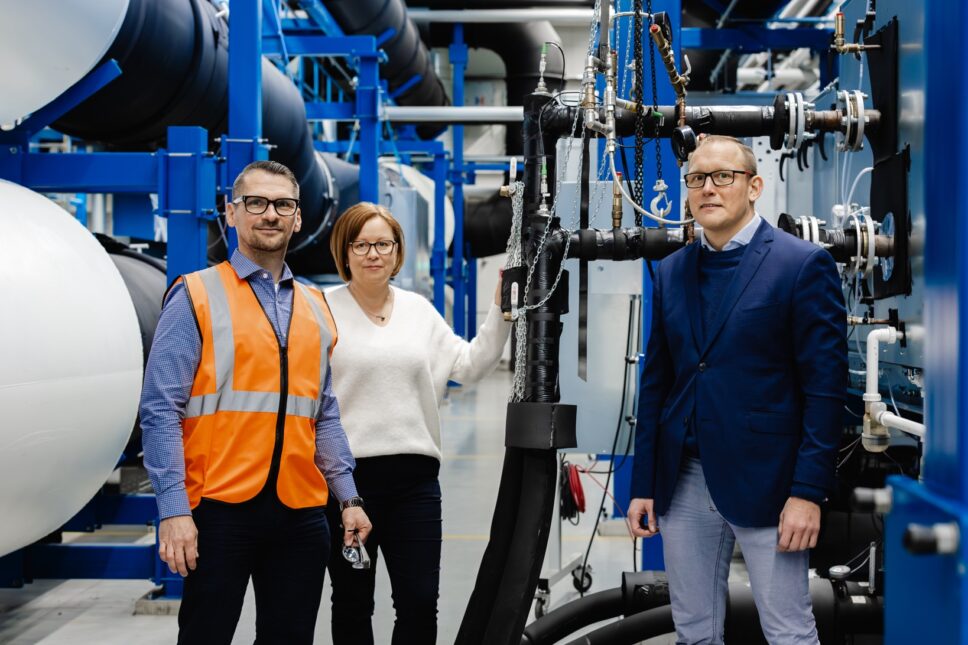
The Koja Group, based in Tampere, Finland, serves large, listed companies in Finland, the rest of Europe and the US by helping them reduce their emissions. “The green transition evolves from our clients’ strategies to our projects,” says Pasi Lähteinen, Business Director of Industrial Solutions at Koja. Koja has invested significantly in technology and technological developments.
The green transition and sustainability inform the entire strategy of this family company, which has grown from a small Tampere metal workshop into a global player. Its investments in recent years in the technology and RDI to support this have borne fruit. The group, based in Tampere, Finland, serves large, listed companies in Finland, the rest of Europe and the US by helping them reduce their emissions.
“We want to be a technological and environmental leader in our sectors. We want to be a beacon our clients can trust when they need air handling solutions for ships, industry or buildings,” says Pasi Lähteinen, Business Director of Industrial Solutions at Koja. He is also the CEO of Koja USA Inc.
The company has seen its work deployed on a large scale.
The world’s largest cruise ship, the Icon of the Seas, was built in Turku in November. Its air handling units (AHU) were from Koja. In Indonesia, the group has skin in the game in huge investment projects related to industry’s decoupling from coal. Koja also has a strong foothold in European heat and electricity generation facilities. It is involved in a significant number of heat and electricity plant projects which seek energy efficient solutions for new and existing facilities.
“The green transition evolves from our clients’ strategies to our projects,” Lähteinen says.
In addition to its global Marine and Industrial Solutions businesses, Koja Group also provides air handling solutions for buildings, mainly for the Finnish market.
Green approaches in collaboration with clients
Koja invests in working with clients to improve their outcomes. In the company’s Industrial Solutions business, clients use Koja products in energy production and various glass manufacturing processes intended for buildings and vehicles.
“We strive to work with our clients to find the most energy-efficient solutions and greenest approaches to their processes. In addition, our technologies strongly support security targets,” Lähteinen says.
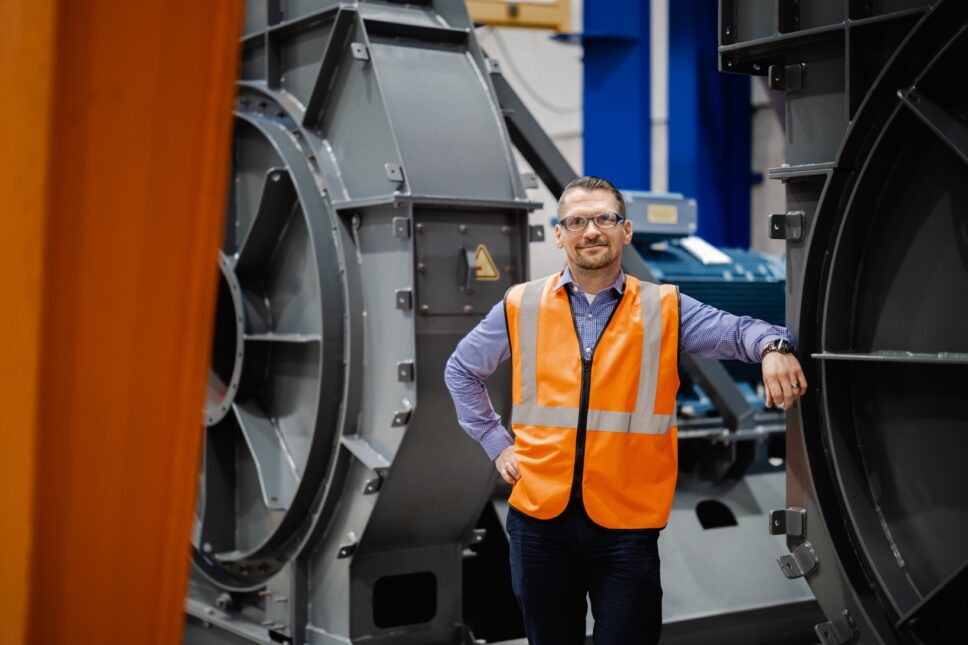
For example, when Koja manufactures its industrial machinery out of composite structures rather than steel, it raises human safety, usability and noise management to a new level.
Energy is also saved, as in new composite-structure glass tempering processes, large industrial fans and motors can be shut down during the phases in which they are not needed and correspondingly ramped up quickly. Previously, the steel structures used at plants had to be kept constantly running.
Lähteinen has a recent example from the US. A Koja client had managed to use the new Koja technology to save energy in its glass tempering process by 20%.
“They said they couldn’t find an equivalent service anywhere else. You can usually shave half a per cent or one per cent off energy consumption. Being able to save that much energy across an entire plant is unprecedented.”
Waste recycling and bio-heating plants
Koja works closely with waste recycling and bio-heating plants in Europe, which have the clear goal of transitioning away from Russian natural gas and all coal. The number of waste incinerators in Europe has increased and continues to increase. They can make good use of household waste and convert it to heat.
“Our products also play a significant role in the waste drying process and in reducing the sulphur and carbon dioxide emissions from flues,” Lähteinen says.
Koja is also involved in projects in which raw materials are made as low emission and optimal as possible when they enter processing.
Serving the world’s largest cruise lines
Koja’s clients include the world’s largest cruise lines, Carnival Corporation & plc, and Royal Caribbean Group, which account for 80% of the world’s cruise ship capacity.
“The air conditioning system on board giant cruise ships consume a lot of energy. With our new technological solutions, smarter navigation, and automation, these giants can continue to make big energy savings,” says Teemu Tanninen, Business Director of Koja’s Marine business.
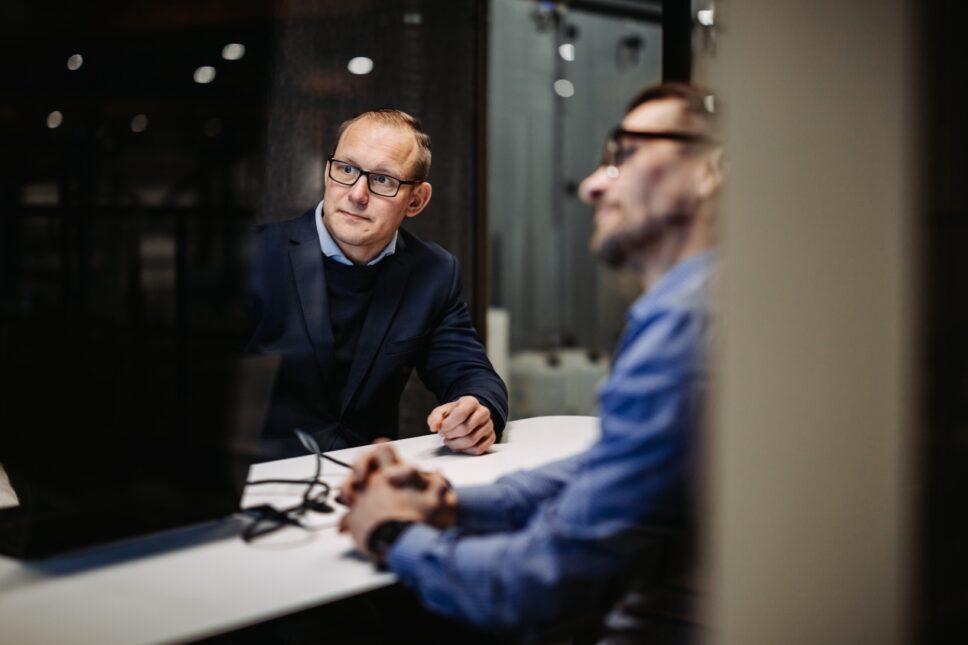
The IMO´s energy efficiency requirements in force since the start of 2023 also apply to existing ships — not just new ones, as previously.
By March 2024, shipping companies must report fuel consumption figures and nautical miles sailed for each vessel to the authorities. On that basis, a carbon intensity indicator will be calculated for the ships.
“If the result isn’t good enough, the shipping company will have to come up with new ways to reduce fuel consumption or, on the other hand, shorten the cruise, which nobody wants,” Tanninen says.
Thus, means to cut fuel consumption must be found. On a cruise ship, air conditioning accounts for 10–15% of overall fuel consumption, depending on the system and the ship’s cruise profile.
“We’re confident that we can use our new technologies to reduce the energy consumption of air conditioning by up to 25%,” Tanninen says.
In the future, effort will also be made to fit ships’ air conditioning system in a more sensible statistical fashion, that is, to cover 99% of all conditions, making the system more energy efficient. At present, they are designed for conditions which occur only few times a year.
New €10M investment programme
Koja continues to make sizeable investments in its technology and in improving it. A few years ago, Koja invested €30 million in its Tampere factory and its R&D Center. The group has just invested €10 million in a factory in Jalasjärvi in western Finland.
“We’ve conducted investment programmes to the tune of tens of millions of euros which have supported our technological progress. Currently on the table is a €10 million programme which we will implement over three years,” Pasi Lähteinen says.
The Koja R&D Center in Tampere is capable of measuring both the heating properties of AHU in the winter and the performance of equipment in the Caribbean.
“R&D is a significant part of what we do. It represents a significant share of our turnover, which will grow in the future,” Teemu Tanninen says.
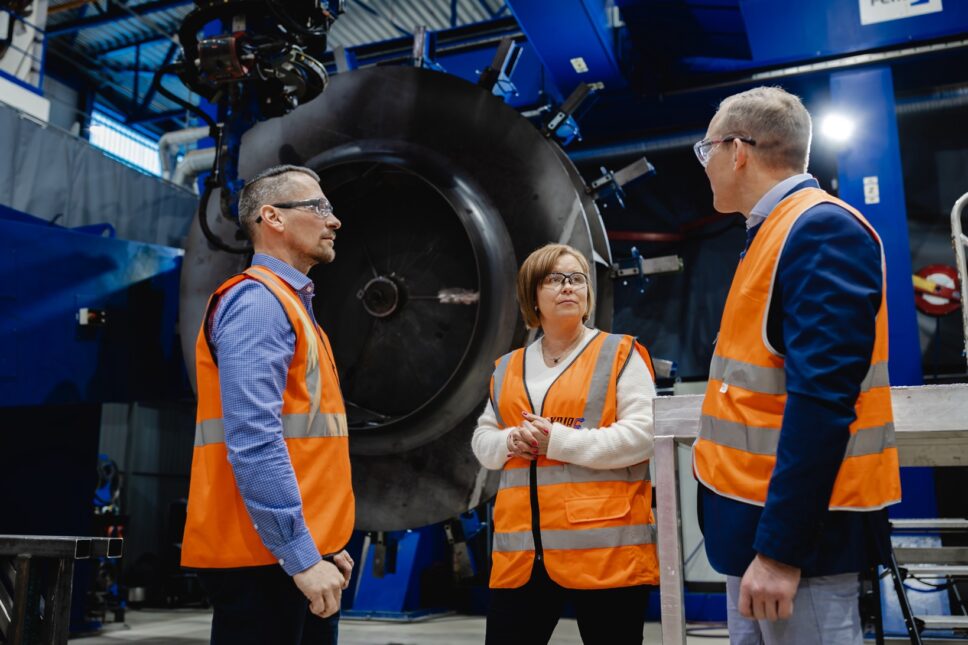
A new technological centre is already being designed. It will be built in Tampere and focus on R&D and testing opportunities for industry products.
The goal is to heat it and the entire Tampere premises geothermally in the future.
“That will make us self-sufficient in terms of heat. On top of that, we’re striving to generate a significant share of our electricity with solar panels. These things are at the heart of new projects. We’re correcting the current situation, too. We study where and how our energy consumption can be as low as possible. In addition, we pay attention more generally to recycling and material waste,” Lähteinen says.
The Tampere production plants already use renewable electricity. At night, energy consumption is reduced through measures such as lowering the pressure of compressed air and optimizing ventilation. In the new production units built in Jalasjärvi at the start of the year, there are rooftop solar panels, and energy consumption has been highly optimized.
End-to-end sustainability in the value chain
Sustainable thinking is also an integral part of Koja’s own procurement and logistics chain.
“We factor in our suppliers’ sustainability are and strive to pay attention to the carbon footprint of logistics. We form reduction targets by calculating our products’ carbon footprint,” Development Director Johanna Kärki says.
“A large proportion of our industry and marine solutions are exported, but we also make good solutions of the same kinds for the Finnish market,” Koja Group’s Development Director Johanna Kärki says. “Requirements are constantly increasing, both by us and of us. That’s how a sustainability chain forms,” she says.
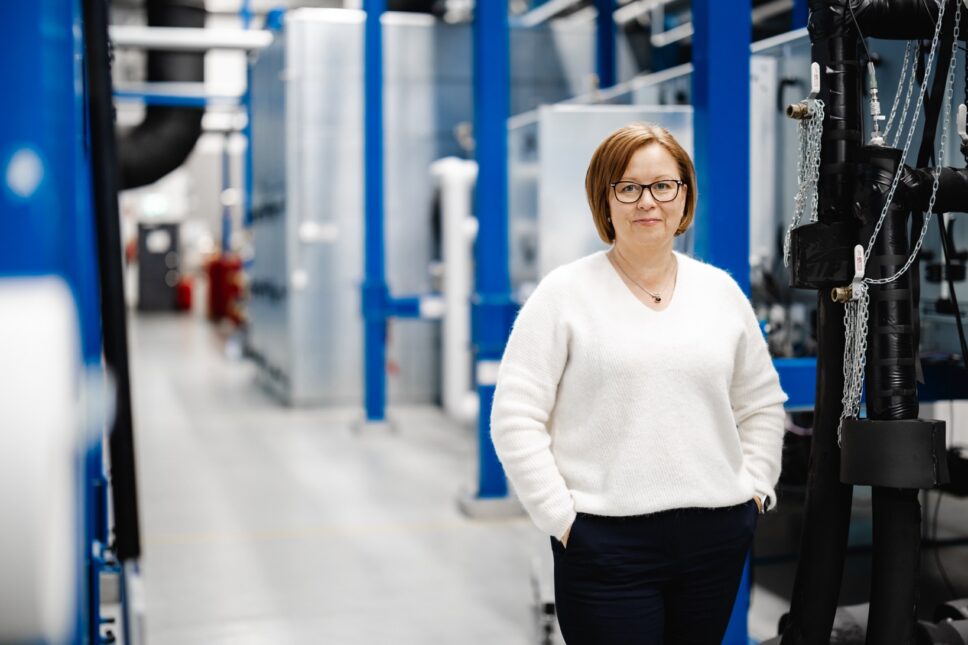
Sustainability is already crucial for large companies. Kärki also considers working with smaller subcontractors important.
“We can work in an agile fashion with them and enhance our collaboration.”
If a small company does not have source data or a sustainability culture, Koja strives to develop sustainability with it: in occupational safety and health, in raw material use and in logistics.
In the Marine business, the company intends to develop a calculator for cruise ships and ferries to assess their HVAC system life-cycle energy consumption.
“The initial investment in a system which uses less energy is usually higher, but with the help of the calculator we are able to review the life-cycle costs of an air conditioning system with our clients. This will assist the ship owner’s decision towards more energy efficient and therefore greener technology,” Teemu Tanninen says.
€1M occupational safety and ergonomics
Sustainability also unites the everyday work of the company’s employees and in-house process development.
In Tampere, a €1 million investment programme in occupational safety and ergonomics is underway.
“We’re constantly developing that. Work involving vibration is being phased out, working postures are being improved, and we’re reducing the amount of climbing to heights done on the job,” Lähteinen says.
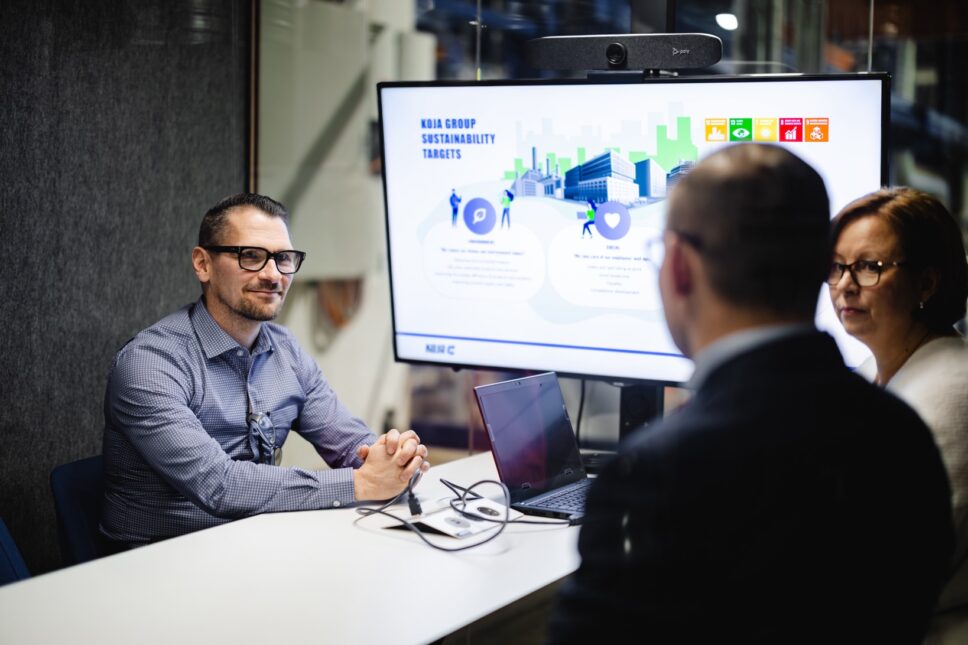
Development Director Johanna Kärki is pleased with the low number of occupational accidents. At the Tampere location, there has not been an accident requiring absence from work for over a year. Employees receive thorough job orientation, and they are involved in improving the safety, manufacturing methods and technologies of their work.
“Responsibility begins where the law ends. All of these things are choices and the will of our company. If we only did what was compulsory, we wouldn’t be where we are now — not in products, not in anything else,” Kärki says.
Text: Marjo Vuorinen
Photos: Matias Ahonen