Technology from Turku solves industrial energy problems around the world – Converting side streams into new products for global markets
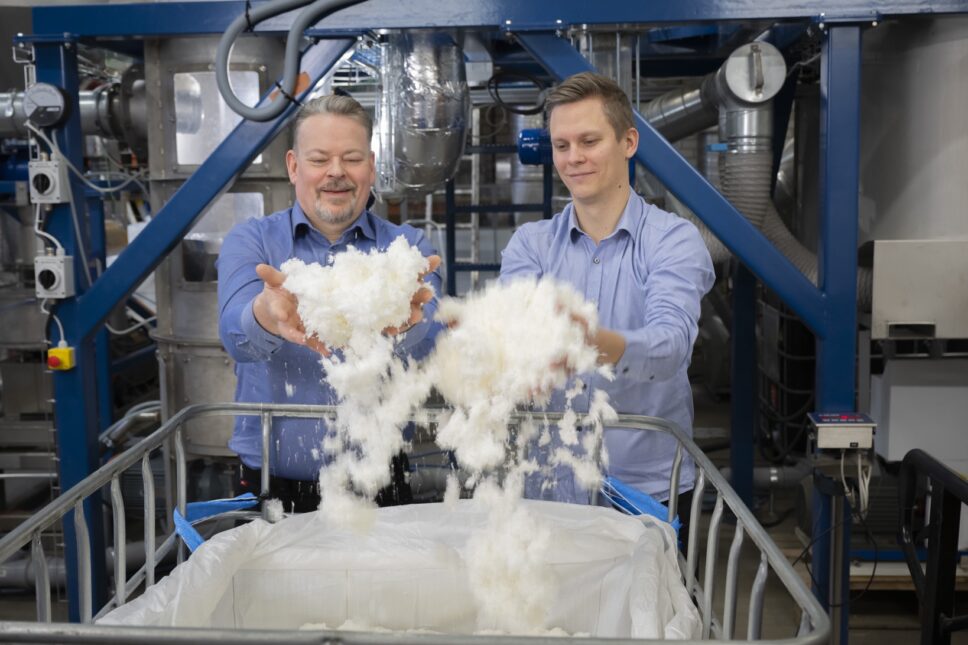
Industrial side streams can offer new business opportunities for companies capable of looking at their waste and side streams in a new light. TM System, based on Turku, makes technologies that reduce companies’ emissions and address their raw material and energy production problems. The group’s parent company invests in research and development, and the new products have brought the company closer to Finnish businesses.
TM System has provided services for industrial air systems, energy saving, heat recovery and drying technology for 50 years. It serves paper and pulp industry operators in Asia and South America, but its clients also include the Finnish forestry giants.
- TM System Finland Oy provides services for industrial air systems, energy saving, heat recovery and drying technology, especially for the paper and pulp industry.
- New technologies are now carrying the company into other industries.
- Headquarters in Turku but customers globally.
- Established in 1974.
- A total of 90 employees throughout the group.
- The group’s net sales reached EUR 25.9 million in 2022, and its profit was EUR 3.1 million
The new technologies developed by the company – Zero-Ex, which aims for a closed process air circulation and zero emissions, and SuperDryer, a drying technology – have brought the company closer to Finnish and European businesses, as its scalable solutions enable production plants to be smaller and more local than before.
“The problems are global. The same things come up in discussions with customers in Japan and China as in Finland,” says Markus Hallapuro, the company’s main owner.
The world will be transformed over a decade
Topics that connect different types of companies are related to emissions, energy production and sources, raw materials and logistics. Every company in the world will need to think about its emissions and report on them in the near future. Production requirements and emission restrictions will guide operations.
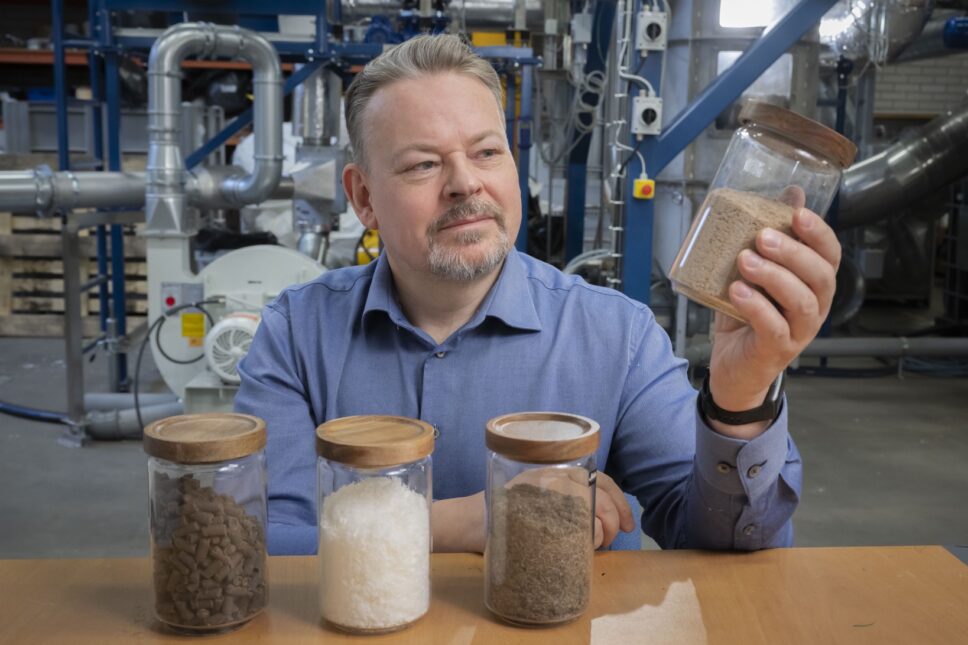
In addition, world events, such as Russia’s invasion of Ukraine, prompted companies to think about energy production and sources. Forest biodiversity and logging are important topics in Finland. According to Hallapuro, mindsets are changing.
“A lot will change over the next decade. People are starting to think about where new biomass will come from. How will it be made? How will it be moved? Bio-based raw materials are also obtained from many side streams of industry and agriculture,” says Hallapuro.
New technologies enable biomass to be used as cellulose, for example. Biomass-derived material has multiple further uses, including for the needs of the pharmaceutical, cosmetic and food industries.
“People generally want to replace fossil-based materials such as plastic with bio-based materials.”
New solution reduces emission to zero
The rapidly advancing changes require new technological solutions like TM System’s Zero-Ex and SuperDryer.
Zero-Ex is a patented technology that enables the closed recirculation of process air, minimising emissions and maximising energy efficiency.
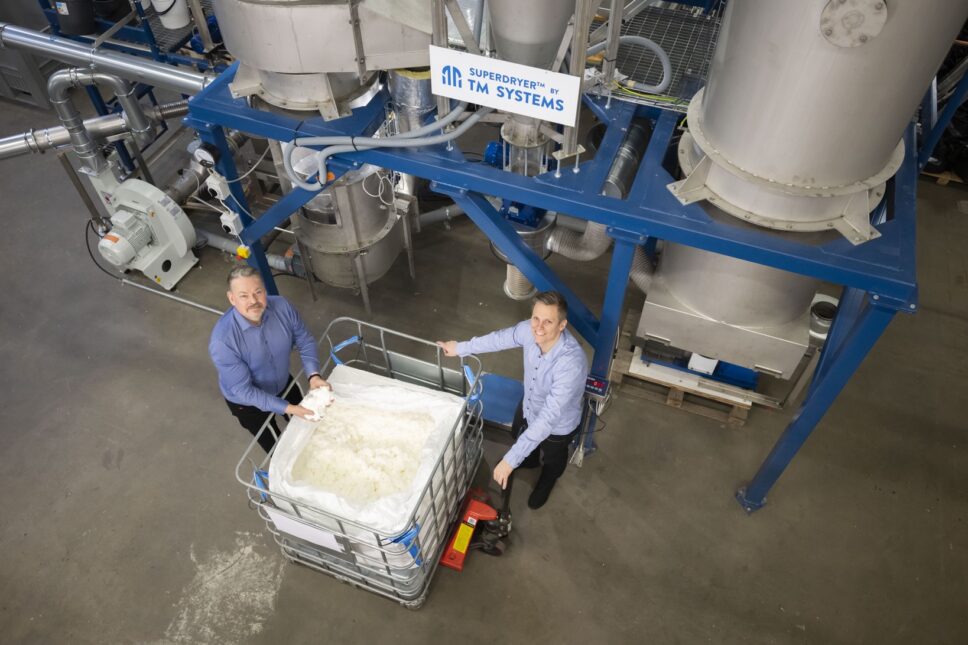
Eeva-Maija Hallapuro, Partner and Board Member at TM System involved in business development, describes an example in China where a factory emits steam and a nasty odour, disturbing nearby residents, so the authorities intervene. A Finnish forestry giant had a similar problem in Southern Finland, but thanks to Zero-Ex, odours and emissions were completely eliminated.
“Often, the initial problem is an odour or visual issue. When the issues are examined in more depth, bigger problems emerge, calling for improvements in the process. Our technology enables production to continue despite strict regulations on emissions,” says Eeva-Maija Hallapuro.
Zero-Ex was awarded the Finland Futures Research Centre’s Future prize at Empowering Future, a science conference held in summer 2023. The prize is awarded for research into a visionary solution that transcends societal sectors and supports the construction of a more sustainable global future.
“The closed circulation loop allows for a completely emission-free plant where the water consumed by the process can be pumped back into the process instead of evaporating into the open air. Air and water are natural resources that are monitored more closely, and efforts are made to purify and recycle them,” Markus Hallapuro says.
“Our technology saves our customers about 10 terawatt hours a year, so there is the potential for significant energy savings.”
He gives an impressive example.
“The annual output of the Olkiluoto 3 nuclear power plant is about 12 terawatt hours. Our technology saves our customers about 10 terawatt hours a year, so there is the potential for significant energy savings. You do not always need to produce new energy.”
Industrial waste is valuable material
Industry, households and businesses produce waste, biomass and side streams that can and should be used and recycled more effectively than today, as they are valuable materials.
Before Russia invaded Ukraine and before the Dubai climate conference, the need for biomass was expected to increase by 70–150 per cent by 2050. Since then, the need has only increased.
Dried biomass and side streams could be used as new raw materials, recycled fibres, soil conditioners, and fertilisers compressed into fuel pellets.
SuperDryer is the key to viable drying, as it scales as needed.
“Biomass production is becoming more local – smaller biogas plants are springing up around the country to ensure the security of supply,” Hallapuro says.
Industrial operators have often seen drying as one more burdensome expense rather than examining its role more critically.
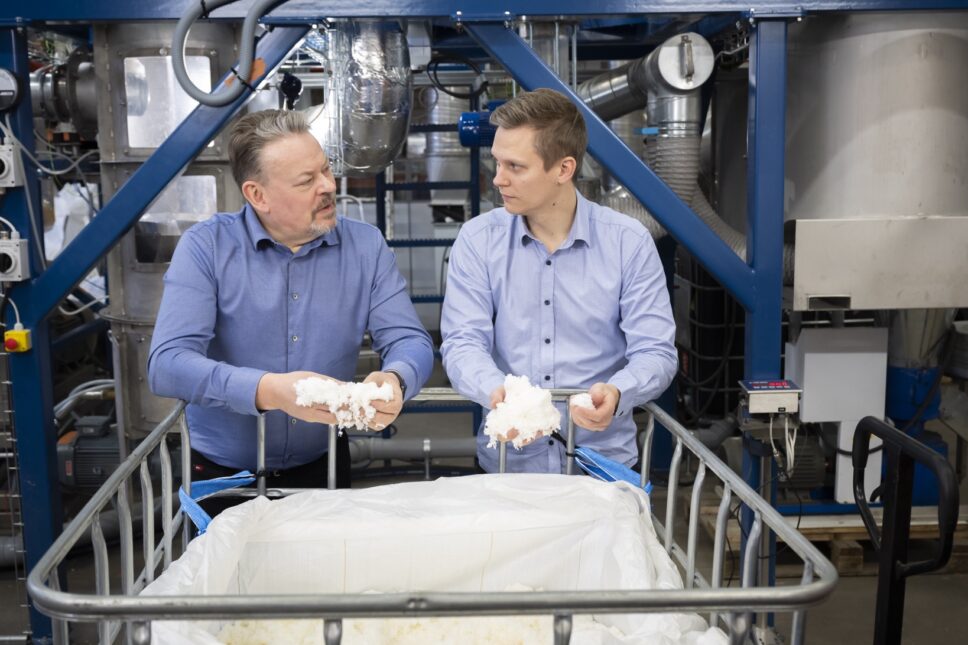
“Side streams are often difficult to process because it is hard to find a sensible and financially viable way to organise production around them.”
A wet product can spoil quickly, and the mass can be up to 60–70 per cent water, which is unprofitable to transport. Dry products have new applications and global markets, and a dry pellet does not rot during transit.
“There is a lot of recycling in Finland, but processing methods could still be improved. Ninety-four per cent of side streams from the Finnish forestry industry are utilised, but the degree of processing is low. For example, wet sludge is disposed of by incinerating it in a bio-boiler,” Hallapuro says.
If the mass were dried, it could have new applications, and it could be processed to create a higher-value product.
“If we fail to recognise the value of side streams, they will only have a negative impact on factories. A potentially valuable material could end up on a compost heap, emitting greenhouse gases. A dried product presents a wealth of new opportunities.”
One-third of personnel work in research and development
SuperDryer technology and Zero-Ex were both inspired by customer needs. The Hallapuros say that research and development has been self-sufficient, but some of the rolling business earnings have been allocated to cover the research and development expenditure.
SuperDryer received substantial development funding for the pilot project and scaling from the EIC Accelerator programme administered by the European Innovation Council. The EIC Accelerator programme has strict rules for awarding funding, and only 2.5 per cent of applicants are successful.
The company is now launching a project supported by Business Finland.
“We always have a target for our research and development work. It is always based on a clear need derived from problems affecting customers or a customer market,” Markus Hallapuro states.
TM System invests approximately 4 per cent of the group’s revenues of EUR 26 million in research and development. About one-third of the 36 employees at the group’s parent company are involved in research and development. Half of them focus on research and development full-time, while the remainder are involved via project work and sales.
“People in customer-facing roles need to understand the customer’s business and process and realise which problems have yet to be solved. Zero-Ex began as a single product but has since expanded into a product range. SuperDryer was born of one customer’s need. Since then, the market has expanded exponentially, as we realised that this is an urgent and global problem across many industry sectors,” Hallapuro says.
Customers interested in the test facility in Turku
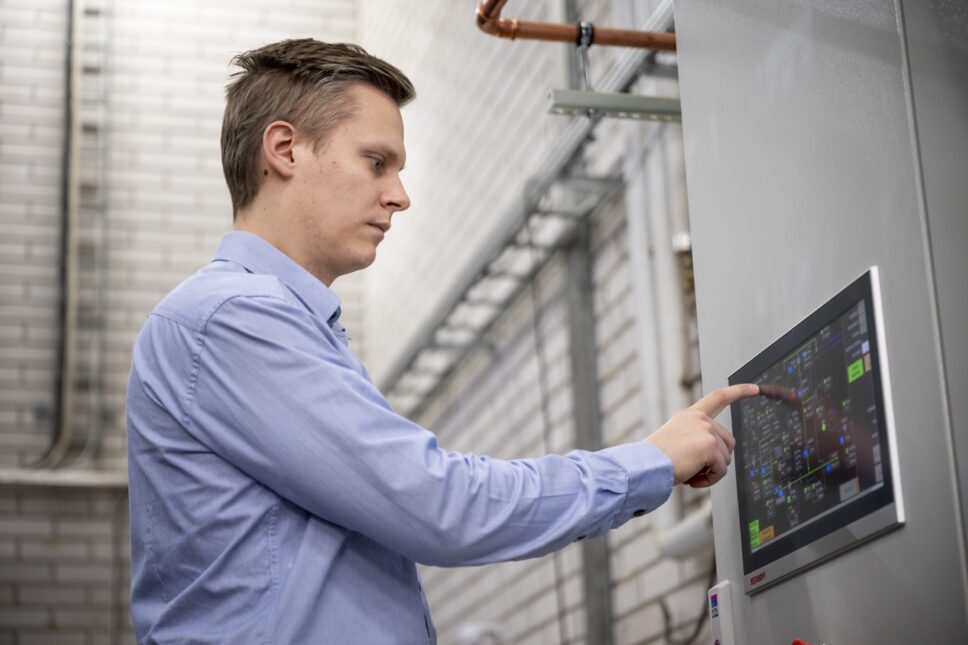
TM System has customers on every continent and a unique test facility in Turku, Finland. The test facility interests customers, stakeholders, researchers and students alike.
“Customers are interested to see whether their raw material can be dried,” says Eeva-Maija Hallapuro.
The test facility is run by Aleksi Hidén, the Product Manager of the SuperDryer technology. He meets current and potential customers and tests their products.
“The tests reveal what the mass is like when it is dried and how it behaves. Customers are interested in characteristics such as weight, stickiness and drying speed. It is important to optimise the process parameters to suit the to-be-dried mass provided by the customer,” Hidén says.
Experiments show how energy-efficient drying can be. This serves internal product development and helps with brainstorming.
“We have a small industrial-scale plant in Turku where we can replicate genuine process conditions,” Hidén says.
TM System’s Zero-Ex air treatment technology is also tested at the test plant to gauge how it eliminates dust and odours and recovers carbon dioxide.
Text: Elina Hakola
Photos: Vesa-Matti Väärä